蒸餾是將液體混合物部分氣化,利用每組分揮發度的不同特性來達到分離的目的。在蒸餾過程中使用羅茨真空泵之前,存在以下問題:較長的蒸餾時間,超過12h
/批;許多蒸餾殘留物。其原因在于,由于在蒸餾過程中使用的時間長且蒸餾溫度較高,因此蒸餾后的焦化樹脂——的量相對較大。那么如何解決這個問題呢?下面將介紹蒸餾過程的分類以及羅茨真空泵在蒸餾過程中的應用。
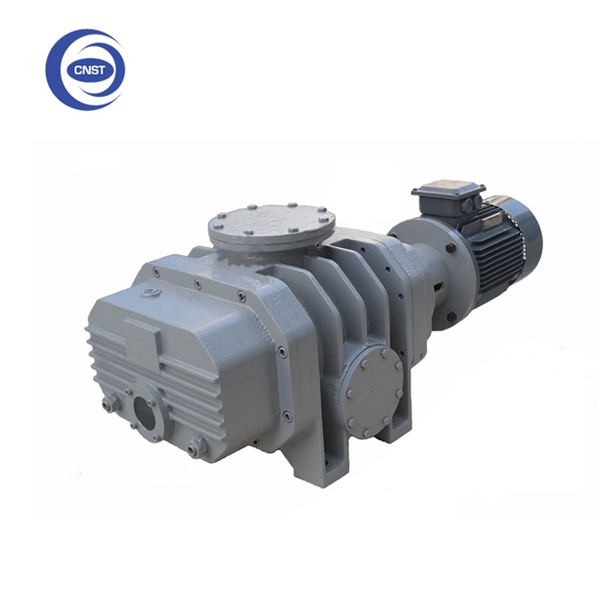
蒸餾過程通常分類如下:
①根據被蒸餾混合物的成分數量,可分為二元蒸餾和多重蒸餾。
②根據操作過程是否連續,可分為間歇蒸餾和連續蒸餾。
③根據工作壓力可分為常壓蒸餾,壓力蒸餾和真空蒸餾。
④根據操作方式可分為簡單蒸餾,平衡蒸餾和精餾。
⑤根據分離系統的一些特殊要求,精餾還包括蒸汽精餾分批精餾,共沸精餾,萃取精餾,反應精餾等。
蒸餾是熱力學分離過程。它利用混合液體或液體-固體系統中組分的不同沸點來蒸發低沸點組分,然后冷凝以分離出整個組分。它是蒸發和冷凝操作單元操作的聯合體。與其他分離方法(例如萃取,過濾和結晶)相比,它的優點是不需要使用系統組分以外的其他溶劑,從而確保不會引入新的雜質。
為了解決上述問題,經過分析研究,我認為應該從提高真空度的角度考慮。從理論上講,高溫將加速材料的樹脂化,而較長的材料停留時間將增加樹脂的量。提高鍋內的真空度無疑是解決蒸餾時間長和蒸餾殘渣過多的兩個問題的最佳方法。
首先,可以在增加真空度之后降低材料的沸點,即,降低蒸餾操作中的起泡點溫度。其次,增加真空度可以增加蒸餾的驅動力并加快材料的蒸發速率。
在蒸餾過程中,我們過去使用的真空設備是普通的無油真空泵。現在采用的方法是與無油真空泵串聯使用羅茨真空泵的高真空。我們知道無油真空泵吸進了系統。它是羅茨真空泵的廢氣。在羅茨泵的幫助下,保護箱上的真空度大大提高,空載運行時的真空度幾乎為-0.1Mpa。
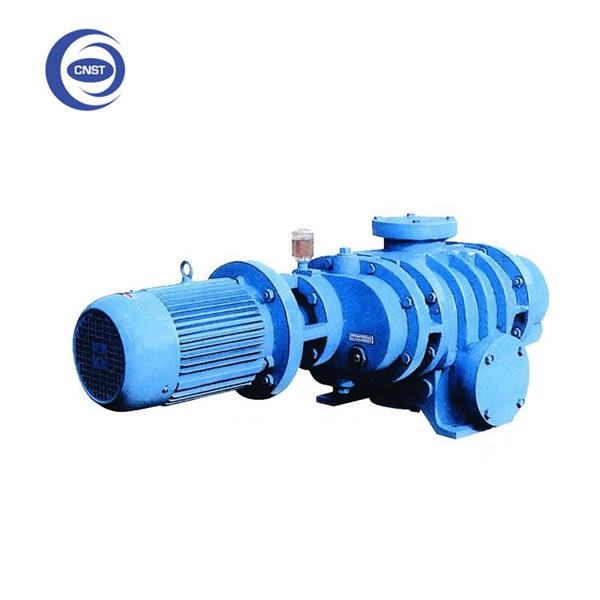
在實踐中已證明將羅茨真空泵應用于蒸餾過程中,高度真空有利于氯化鎂和鎂的蒸發,也有利于減少氣體污染。真空蒸餾過程后期的真空度要求不大于0.013Pa。同時,可以提高回收率,增加回收量。此外,將羅茨真空泵與無油真空泵串聯使用可有效縮短操作時間并減少樹脂殘留量,從而減少產品的原材料消耗。